Surface treatment plays a vital role in improving the durability, aesthetics and functionality of aluminum panels, including aluminum honeycomb panels. The surface treatment methods of aluminum plates include roller coating, powder spraying, plastic spraying and other techniques. Each method has unique advantages and disadvantages, and understanding its process and corresponding products is critical to selecting the most appropriate treatment method for a specific application.
Aluminum honeycomb panels are widely used in the construction, aerospace, marine and transportation industries due to their lightweight nature and high strength-to-weight ratio. The surface treatment of aluminum honeycomb panels is crucial to ensure its performance and service life in different environments. Let's take an in-depth discussion of the surface treatment methods of aluminum honeycomb panels, analyze the advantages and disadvantages of roller coating, powder spraying, and plastic spraying, as well as their ideal use environments and examples.
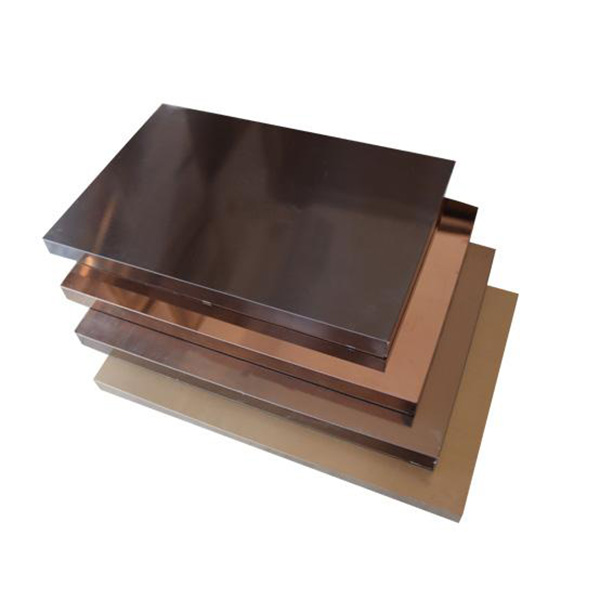
Roller coating:
Roller coating is a surface treatment method that uses a roller to apply liquid paint to aluminum honeycomb panels. This method offers several advantages, including uniform coating thickness, excellent adhesion, and the ability to achieve a variety of surface treatments, such as matte, glossy, or textured surfaces. In addition, roller coating has good corrosion resistance and can be applied to complex shapes and designs.
However, roller coating has some limitations. It may not be suitable for obtaining very thick coatings, and the process may be very time-consuming for large-scale production. Additionally, roller coating may require multiple coats to achieve the desired finish, which increases production costs.
Ideal usage environment:
Roll coating is ideal for interior applications such as interior wall cladding, ceilings and decorative elements that require a smooth and aesthetically pleasing finish. It is also suitable for applications requiring custom colors and finishes, such as architectural features and furniture components.
example:
Aluminum honeycomb panels with a roller-coated surface are commonly used in high-end interior design projects, luxury retail spaces and exhibition stands, where premium finishes and design versatility are crucial.
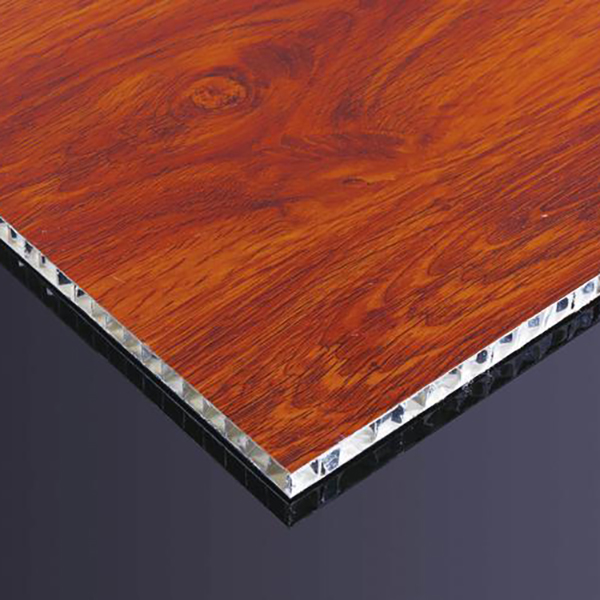
Powder Coating:
Powder spraying, also known as powder coating, is a surface treatment method that involves electrostatically applying dry powder to aluminum honeycomb panels and then curing the powder in an oven to form a durable and uniform coating. This method offers several benefits, including excellent durability, resistance to chipping, scratching, and fading, as well as a variety of color options and finishes.
Although powder coating offers many advantages, there can be limitations in achieving very thin coatings, and the spraying process may need to be carefully controlled to avoid problems such as orange peel or uneven coating thickness. Additionally, the initial setup costs for powder coating equipment and facilities can be relatively high.
Ideal usage environment:
Powder coating is ideal for exterior applications such as building facades, signage and exterior wall cladding that require superior weather resistance, color retention and long-term durability. It is also suitable for industrial and commercial applications that require high-performance coatings with specific functional properties, such as chemical resistance or electrical insulation.
example:
Aluminum honeycomb panels with a powder-coated finish are commonly used in construction projects that require a long-lasting, vibrant finish, such as modern building facades, outdoor sculptures and signage in urban environments.
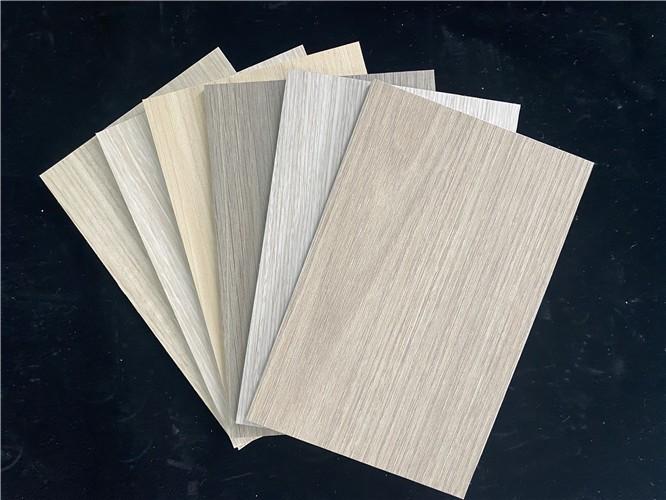
Spray Painting:
Spray Painting, also known as liquid spray painting, is the application of a liquid paint containing plastic particles to aluminum honeycomb panels, which then cures to form a protective and decorative finish. This method offers benefits such as excellent impact resistance, flexibility to achieve different textures and gloss levels, and the ability to create multi-layer coatings for enhanced performance.
However, Spray Painting may have limitations in terms of environmental impact, as some plastic coatings may contain volatile organic compounds (VOCs), requiring proper ventilation and waste management. Additionally, achieving consistent color matching and finish uniformity can be challenging in plastic spraying processes.
Ideal usage environment:
Spray molding is suitable for applications requiring impact resistance and flexibility, such as transportation vehicles, marine components and industrial equipment. It is also used in construction projects where specific design requirements need to be met, such as textured finishes or color gradients.
Example:
Coated aluminum honeycomb panels are commonly used in the aerospace industry for interior components such as cabin panels and overhead storage bins, where a lightweight, impact-resistant and aesthetically pleasing finish is critical.
To sum up, the surface treatment methods of aluminum honeycomb panels include roller coating, powder spraying, plastic spraying, etc. Each has its own advantages and disadvantages and is suitable for different use environments and usage requirements. Understanding the characteristics of each method and its corresponding product is critical to selecting the most appropriate surface treatment for a specific project. By considering required finish, durability, environmental factors and functional properties, designers and manufacturers can make informed decisions to ensure optimal performance and aesthetics of aluminum honeycomb panels across various industries and applications.
Post time: Aug-16-2024